Innovative CQV Solutions
BehinPharma will create a suite of cGMP documents that can be used by the client to provide objective evidence to a regulatory body (CDC, FDA, etc) that the facility or product was built and operates as designed and meets the client User Requirements Specification (URS). These documents include a commissioning plan, FAT/SAT protocols, and a summary report.
Full Commissioning Process
We will take care of everything from user requirement specs, FAT/SAT testing, to IOQ and turnover packages.
Highly Versed Team
Our CQV Engineers are not only specialized in testing our technology, but are also highly versed with the regulatory requirements of the pharmaceutical, biocontainments , and isolation industries.
Onsite Team
Our expert team is located at our manufacturing site allowing full access to the product and other BehinPharma resources from the early design phase through product completion. This allows CQV documents and protocols to be highly detailed and custom tailored to each project.
Collaborative Approach
Client involvement is encouraged during FAT and SAT executions which provides a collaborative approach and ensures thorough and unbiased testing.

Planning for Commissioning
In collaboration with the client, BehinPharma will prepare the commissioning plan for the products and solutions. The plan outlines the scope, tasks, procedures, roles, and responsibilities of various involved groups, and the overall coordination of the commissioning effort.
Our Process
Our CQV process contains a series of detailed tests and supporting evidence that the equipment meets requirements and is executed at our factory following good documentation practices.
Factory Acceptance Testing (FAT)
Commissioning at this phase assures that the product meets customer/design requirements prior to shipment to its final destination. At the factory, every attempt will be made to simulate a completed functioning product to provide the commissioning team the opportunity to test it to the fullest extent possible. This approach minimizes encountering issues onsite and helps reduce site installation time thus expediting the site acceptance testing phase of the project.
Site Acceptance Testing (SAT)
Commissioning at the final destination utilizes a risk-based approach allowing the leveraging of non-critical tests previously performed at the factory and therefore reducing the amount of testing performed on site.
Installation and Operational Qualification (IOQ)
We will author and execute a BehinPharma isolator and equipment testing protocol providing objective evidence that the isolator meets both ISO14644 and FDA-cGMP requirements. The manufacturer of the EMS system will execute their installation and operational qualification (vendor protocol) following installation completion. Finally, we will execute an IOQ protocol for various equipment such as: pass boxes, restrictive access barrier (RABS), gloveboxes and containment systems and provide a summary report.
Turnover Package
At the end of the commissioning process, we will prepare a turnover package that provides a central documentation reference for all systems. This package consists of a combination of documents provided by BehinPharma and their subcontractors. It also includes a narrative summary report of the commissioning process summarizing key information, deficiencies, open issues (if any), and overall results.
Reduced Time To Process Ready
Our CQV services cover all stages of your facility’s lifecycle, from design and construction to operation and maintenance. With a team of highly trained and innovative professionals, we help clients minimize risk, increase efficiency, and maintain compliance, ultimately enabling them to bring safe and effective products to market.
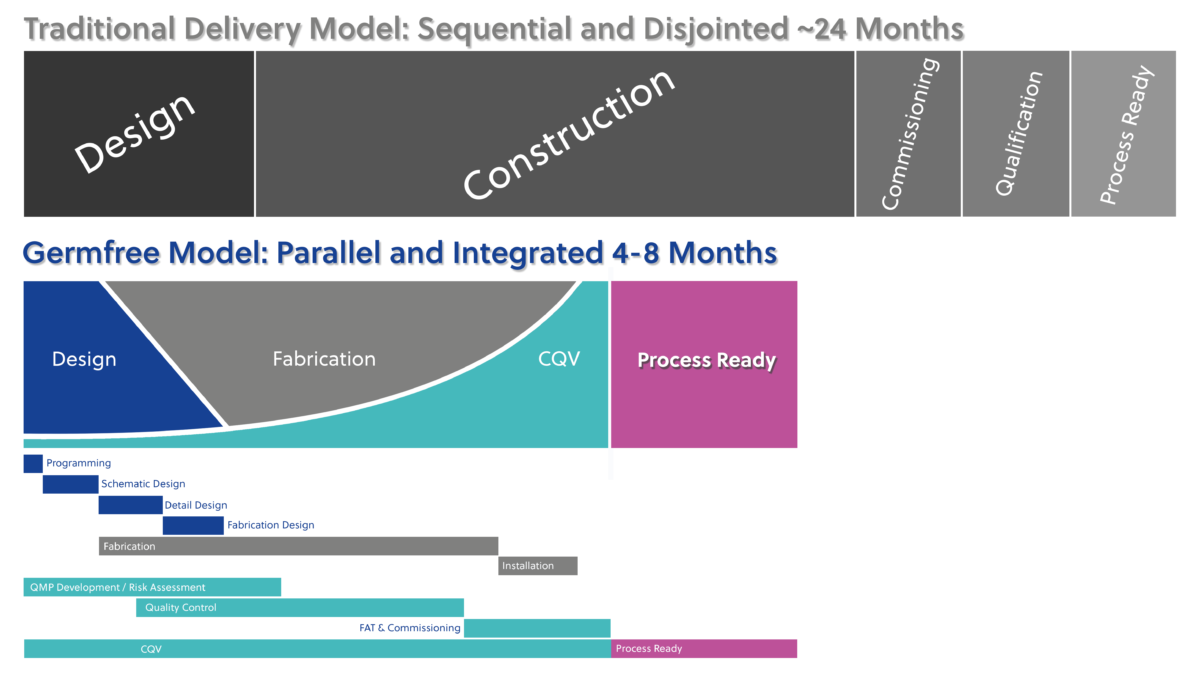